General information
RDP Priority
- P3. Food chain and risk management
RDP Focus Area
- 3A: Agri-food chain integration & quality
RDP Measure
- M04: Investments in physical assets
Beneficiary type
- Producer group / cooperative / farmer’s association
Summary
Kim’s is a local Maltese butcher & wholesaler in Malta, founded as a farmers' cooperative in 1982. In order to keep up with market changes, it sought an opportunity to expand and diversify its production capacity, and to add value to a larger portion of its members’ products in a more efficient manner. CAP investment support was used for restructuring and re-fitting existing unused structures in an abattoir complex and for introducing new cold storage facilities and acquiring the necessary equipment.
Results
- The value of products produced at the plant in Q4 of 2023 was on average 37% higher than in Q1 of the same year.
- Thanks to this investment, the cooperative was able to hire four full-time employees.
- On a weekly basis, the plant can process a maximum of 550 heads, compared to 343 prior to the investment, which is an increase of more than 60%.
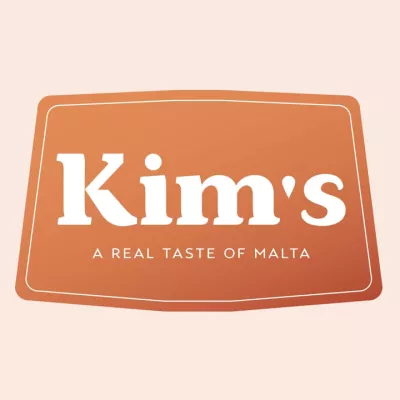
Promoter
Mario Abela / KIM Ltd
Funding
Total budget: 363 373 (EUR)
EAFRD: 109 012 (EUR)
National/Regional: 36 337 (EUR)
Private/own: 218 024 (EUR)
Resources
Documents
Context
Kim’s is a farmers' cooperative representing most of the pig farmers in Malta and Gozo. It was founded in 1982 in a closed market protected by import tariffs. Its role was to help local farmers produce and slaughter pigs and sell them as whole carcasses to local processors and distributors.
The Cooperative has competitors from other EU Member States for its only product, the whole pig carcass. It also faces competition from imported cuts, parts, and market-ready pork products.
Processors stopped contracting with local producers to ensure their supply, so farmers found themselves producing without a guaranteed market. Being limited to whole carcasses restricted the Coop’s potential client base, and gave unreasonable price-setting power to those able to use its one product. It also limited the Coop’s potential earnings and its ability to invest on behalf of its members.
The inability to package and store carcasses meant that pigs could only be slaughtered when sale was guaranteed. When sales dipped, pigs had to be kept on-farm for longer than was viable. To preserve the local pork sector, a stakeholder was required to convert local pig carcasses into marketable products which could be sold at competitive prices to various client types. Kim’s began to invest in cutting and deboning activities in 2010, and has since then continued to expand its capacity to convert, package, store, and transport its members’ products.
Objectives
The objectives of this investment project were to:
- Improve production efficiency to increase the producers’ competitiveness.
- Increase packaging and storage capacity to avoid product losses when sales are not aligned with production due to external market forces.
- Improve the market position and bargaining power of local farmers in the supply chain by offering a wider range of products to meet the needs of a wider range of clients.
- Meet the increasing market expectations for food safety, product presentation and convenient delivery.
- Add value to members’ products to provide the Cooperative with income to invest on behalf of its members.
Activities
Project activities included:
- constructing and installing cold storage facilities. Two chillers and one freezer were added, each with dimensions of approximately 24 m2. Adequate storage capacity allows for the consistent slaughter of pigs regardless of fluctuations in demand for specific parts or products. Whether the product is fresh or frozen, cold storage quality has a marked effect on product quality and product shelf-life.
- investing in packaging equipment. Three vacuum packing machines were purchased. These versatile machines allow the facility to create various package sizes for different clients, and allow the Cooperative to serve clients who are not set up to handle products in bulk. Vacuum-packing is vital to preserve the quality of frozen products and also prolongs the shelf life of fresh products and makes them easier to handle and store.
- investing in increasing the productive efficiency of core processes, such as cutting, skinning, and deboning. This included purchasing: an industrial bandsaw capable of portioning whole carcasses; cutting tables with conveyors to facilitate further preparation of resulting cuts; derinders and chop cutters to facilitate the removal of skin and slicing of loins and collars respectively. A forklift and a palletiser were purchased for moving products around and loading them onto trucks. An automatic knife honer was also purchased to facilitate the sharpening of butchers’ knives.
- investing in an increased product range. This included purchasing a meat injector, a brine mixer and tumbler to enable the production of injected meats for curing, smoking or for use in catering. Sausage mixers and sausage fillers of different scales were also purchased so that the Cooperative could produce a variety of sausages in a variety of volumes. Mincers of different scales were purchased, as well as a mince portioner, to enable the production of minced pork in a variety of volumes, for wholesale and retail.
- investing in increased production capacity. The remaining line items purchased included food-grade plastic and steel containers to store and transport meat and weighing scales (platform scales and tabletop scales) which are used to weigh products during processing or packaging and also at sale. Several stainless-steel tables were purchased to provide suitable working surfaces for a greater number of butchers.
- improving staff facilities to ensure food hygiene and employee safety. Related equipment included boot washers, sinks, knife sterilisers and lockers.
Main results
- Compared to the previously available facilities, this project has increased the total operational area from 317 m2 to 503 m2, while the production area has increased from 249 m2 to 360 m2.
- The product storage area increased from 33 m2 to 81 m2, and carcass storage increased from 35 m2 to 62 m2.
- The hygienic conditions, as well as safety and comfort, have significantly improved both in work areas and staff areas.
- The value of products produced from the plant in Q4 of 2023 was on average 37% higher than in Q1 of 2023.
- Since the completion of the project, the Cooperative has hired four full-time employees at the plant.
- The greatest number of pigs processed in the plant in a single week since the completion of the project was 550 heads, compared to 343 prior to these investments. This is an increase of more than 60%.
Key lessons
- When implementing an investment project it is vital to maintain a project folder from the start and to be conscious of the information required in every document and all correspondence along the way. If some documents from a supplier are missing or incorrect, they have to be recovered immediately, or it may be hard to get these corrected months or years later.
- Project holders should be very specific about functional and material requirements when requesting quotations to ensure that they do not receive offers at a cheaper price that do not meet the required standards. The lowest cost offer presented with the application must be the selected item, or less than 50% of expenditure will be granted.
- Be sure that any purchase agreement or contract for works has a firm date of arrival or completion which is well ahead of the scheduled end date of the project. Project holders should consider and allow for significant variation in international delivery times, as delays of days or weeks are common.
For a producers’ organisation, adding value to members’ products prior to sale helps to ensure that the cost of the organisation itself is not a burden on its members.