General information
RDP Priority
- P2. Competitiveness
RDP Focus Area
- 2A: Farm’s performance, restructuring & modernisation
RDP Measure
- M04: Investments in physical assets
Summary
El Restel is a small, organic, family farm in the province of Verona, Veneto region. Thanks to investment funding from the region’s Rural Development Programme, the owners of the farm (Valentina Tomezzoli and her father, Antonio) managed to purchase a high-tech optical sorting machine to improve their capacity to process the cereals they grow. Having now secured a stronger position in the market by maximising production, the family feels that their business is more secure and sustainable.
Results
Increased product safety and overall productivity.
The farm can now process and package 80%-90% of the cereals they grow (up from 25%-40%).
The optical sorter has reduced the time needed for the control phase of production by 50%.
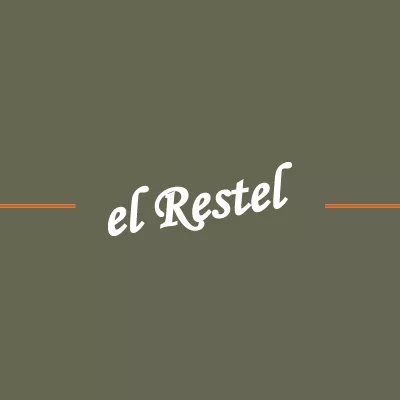
Promoter
Azienda agricola Antonio Tomezzoli
Funding
Total budget 141 364.80 (EUR)
EAFRD 23 431.34 (EUR)
National/Regional 30 908.50 (EUR)
Private 87 024.96 (EUR)
Themen
Ressourcen
Documents
El Restel organic farm - acquisition of an optical sorter for cleaning cereals
(PDF – 2.47 MB)
Links
Context
The El Restel family farm is located in the Verona province of the Veneto region (northeast Italy). The farm grows Vialone Nano, a native variety of rice that enjoys Protected Geographical Indication (PGI). They also produce fruit and cereals that they market either fresh or dried for direct sale to the public. About 15 years ago, the farm completed its transition to organic farming.
The farm has a small facility where the owners process rice, spelt, beans and corn of ancient varieties using traditional methods. Valentina Tomezzoli is the third generation of farmers in the family and has been working since an early age alongside her father, Antonio. Valentina left home to study design in Milano and after earning her diploma, returned to the family farm with the aim of contributing to the business’ development.
Valentina’s university thesis focused on her family’s farm. From her analysis, she understood that the difficulties their business faced were mostly related to the complexities of producing with organic methods. Additionally, their use of artisanal/traditional processing methods – relying on mechanical solutions for the quality control of the products – created additional challenges.
Based on her analysis, Valentina convinced her father to purchase an optical sorter for cleaning cereals; a machine that would ensure high quality standards and improve production efficiency. This type of machine is generally used by industrial companies with higher volumes of production and is very expensive for a small agricultural holding. It was therefore necessary to secure Rural Development Programme funding to enable the acquisition of this new piece of equipment.
Objectives
The main objective of the project was to increase the farm’s capacity to compete alongside larger producers of organic produce. Secondary objectives included increasing safety, improving product quality, reducing processing times and increasing overall efficiency. In addition, by enabling remote control of optical sorting, the farmers have more time to devote to primary activities.
Activities
The EAFRD’s contribution allowed the family to restructure their production facility and purchase the new machinery and equipment that they needed. This upgrade included the acquisition of a state-of-the art optical sorter that can process multiple cereal varieties at the same time. It has two passages through which the grain is channelled by blasts of compressed air. No grain remains in the machine after production as well thanks to its self-cleaning system.
The farmers established a dialogue with specialised technicians, who usually support bigger companies. They were able to share know-how and ongoing support to ensure the correct installation of the machine and the update of its software.
The farmers also made contact with a small start-up company based in the nearby city of Ferrara, from which they eventually purchased the machine.
Main results
Overall, the project has increased product safety on the farm as well as overall productivity, transforming a small agricultural holding engaged in small-scale artisan production into a company that can now compete with bigger, well-established producers.
Before the project, the farm was able to process and package approximately 25%-40% of the cereals it produced annually, whereas now this amount has increased to 80%-90%, with a share of the seeds always saved for planting the following year.
The new machine is able to recognise and process cereals of different shapes and colours, making the sorting process far more efficient by halving the time it takes to conduct the control phase. In addition, the ability to control the machine remotely means that the operator can take care of other tasks on the farm while its sorting.
Key lessons
- It is important to carry out a preliminary analysis of the farm’s specific needs. This can be done by external experts who are able to give an overview of the company’s activities, needs and possibilities for future development. Such an analysis enables beneficiaries to use the available funding in the most efficient way to achieve innovation and growth.
- The successor’s (Valentina) skills were crucial to the success of the project. She dedicated one year and a half to her university thesis, which focused entirely on her family’s farm.
- The investment decision was based on a detailed budget and forecasts of the return on investment.
- Staff training and/or updating is an important part of managing investment in new equipment and processing methods.
- Good organisational skills and the capacity to delegate are essential if beneficiaries are to deal with the administrative aspects of fundraising and project management.
- It is important to take into account the time needed for the actual payment of the funds.
“This project shows the importance of supporting a specific investment (in this case, an optical sorter) when the investment itself is a key component of a complex business project, which aims at improving the ‘global’ sustainability of the enterprise”.
Veneto RDP Managing Authority