General information
RDP Priority
- P1. Knowledge transfer and innovation
RDP Focus Area
- 1A: Innovation & cooperation
RDP Measure
- M16: Cooperation
Beneficiary type
- Small-Micro Enterprise
Summary
The project FILIERA 4.0 addressed the environmental issues concerning the use of polypropylene in the production of plant pots. Promoted by ‘Liguria Digitale’, a small company based in Liguria, Italy, the project aimed to identify innovative solutions for replacing polypropylene with biodegradable and compostable materials. At the same time, sustainable phytosanitary control strategies and a digital traceability system were developed to enable supply chain actors to offer a reliable, traceable ‘clean, plastic-free and ‘zero residues’ product’. The project also attended to relevant product certification processes to enhance the link between production and territorial development. The project actions enabled partners to experiment and develop technical solutions designed to increase the value of the production of plant pots in the Liguria area involving different types of flowers and vegetables, as well as aromatic plants.
Results
- A Digital Supply Chain Traceability System was created. It is based on a platform, and integrates different media in an innovative manner. The system is administered by Liguria Digitale.
- Participating farms diversified their products and increased their sales from September 2021 onwards, resulting in their increased economic sustainability.
- An increase in the efficiency of the production and distribution processes was achieved.
- Marketing capacities were enhanced, and the environmental impact of agricultural activities was reduced.
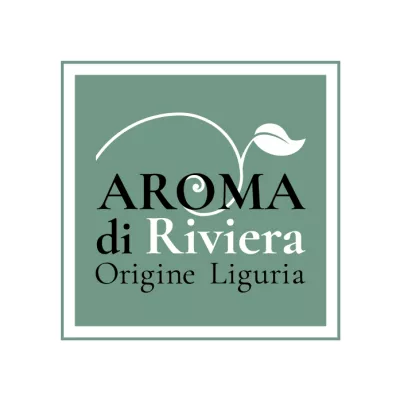
Promoter
Liguria Digitale
Funding
RDP support: 399 191 (EUR)
Ressources
Documents
Context
Increasingly, consumers seek reassurance about the phytosanitary condition of the food and plants that they buy. The challenge for growers, producers and retailers is to prove that they are offering a “clean” product. To address this challenge, sustainable phytosanitary control strategies and the adoption of a “progressive” supply chain approach could effectively encourage growers and farmers to reduce and ultimately end the use of pesticides. Farms would then be able to demonstrate that their products have zero pesticide residues. To achieve this aim effectively, the entire supply chain needs to be involved in order to offer product certifications that rely on the traceability of all operations. In support of this ambition, the development of accompanying territorial development strategies would further strengthen the links between production and the relevant stakeholders across the territory.
Building on these needs and opportunities, the project concept of replacing polypropylene in plant pots with more environmentally friendly material was generated by a small company called Liguria Digitale, located in the Liguria Region of Italy. Important cooperation partners included CeRSAA (a science organisation), and the operational partner Cooperativa L’Ortofrutticola. The project was built on an agreement developed and signed among the main agricultural cooperatives in the Liguria region (over 800 members), the agricultural trade unions, and several traders of potted plants, focusing on supporting environmentally sustainable, territorial development, and food safety.
Objectives
The objectives of the project were to replace polypropylene by using plastic-free, natural materials. The specific aim was that the new pots would break down into their natural components at the end of their use, thereby increasing soil fertility and preventing waste production.
The project also aimed to achieve ‘zero residues’ by reducing the numbers and amounts of residues of pesticides and encouraging growers to achieve zero residue production.
In addition, the project sought to provide farmers with technological support, IT tools, and innovations that would offer added value in the traceability and easy recognisability of products and their components.
Activities
The first phase of project activities involved the identification of a biodegradable/ compostable material. It was called "Material 5", and based on thermoplastic starch and other constituents, suitable for containers used in common horticultural and agricultural production. Importantly, the new material needed to be tested according to its durability, consistency in mechanical performance, colour stability, and the overall visual quality of the end product. Here, it was relevant that the results would demonstrate that the new material was visually comparable and competitive with similar manufactured polypropylene or other synthetic plastic pots. Following the tests, the project proceeded with the final commercialisation stage.
With regard to fostering zero residues of pesticides in crops, the project activities involved analysing the production specifications for aromatic and officinal/medicinal crops in Liguria, and identifying those agrochemicals that were compliant with officinal crop production. The project further explored the expectations of retailers in terms of the maximum number and quantity of residues in marketed crops and how these requests could be accommodated in a realistic manner. This was followed by setting up cultivation protocols and analytical compliance monitoring procedures, including risk assessment. The designing of a zero-residue certification scheme in conjunction with an integrated production approach followed.
Finally, the project activities focused on traceability and brand identity. Key activities included studying and analysing the reference market in order to proceed with drafting technical specifications for the creation of the project platform, and the subsequent evolution of the project website. Creating and using the brand, accompanied by the development of the traceability system, has been the subject of experimentation throughout the design life cycle, so as to maximise the visibility and recognisability of the project. In line with the supply chain approach, the target audiences included farmers, manufacturers, retailers and distribution centres, traders, certification bodies, researchers and consumers.
Four pilot farms were involved in various operational phases: the creation of the brand, the use of the QR code for the traceability of the products, and the experimental use of pots made of alternative materials.
Main results
- A Digital Supply Chain Traceability System was created based on a platform integrating different media in an innovative manner. The System was composed of a web interface with reserved access for manufacturers to upload information, and a specific section of the project website for member farms and products. The system was administered by Liguria Digitale.
- Participating farms diversified their products and increased their sales from September 2021 onwards, resulting in their increased economic sustainability.
- An increase in the efficiency of the production and distribution processes was achieved, based on a production cost analysis conducted in the second year of the project.
- The trust between producers and consumers was increased due to the number of interactions, contacts, and comments collected at communication events and through communication platforms.
- Marketing capacities were enhanced according to a market analysis involving consumers and commercial intermediaries.
- The environmental impact of agricultural activities was reduced.
- Further commercial trials were planned in 2023/2024 in at least five other Italian flower-growing areas.
- Many students from local agricultural high schools were involved, trained, and employed in field investigations on the quality of plants grown in compostable pots.
Key lessons
- Innovative products need to be economically viable and competitive to succeed in the market. The project showed that business profit can be achieved by leveraging environmental and food innovation.
- Innovative projects must have a large experimental component to succeed. After lab tests, field tests are needed, while success is unlikely without the direct participation of farmers.
- Successful, compostable product development relies on a solid and extensive pre-industrialisation experiment.