General information
RDP Priority
- P2. Competitiveness
RDP Focus Area
- 2A: Farm’s performance, restructuring & modernisation
RDP Measure
- M04: Investments in physical assets
Beneficiary type
- Small-Micro Enterprise
Summary
The project supported the ambitions of the small- to medium-sized honey producing and exporting company 'Medas' to maintain its high-quality production facilities. The family business is located in the region of Spišská Nová Ves in Slovakia and counts today among the largest domestic honey trading companies, sourcing honey from across the entire country. The project activities aimed at improving the processing technology used to make a range of honey products, maintain high-quality production standards, achieve high customer satisfaction levels and increase business sales.
The project activities included improving the production facilities to address a number of construction modifications on the perimeter shell of the building, including energy efficiency measures, and procuring a range of technical equipment to support the modernisation of the production process. This included items such as a crystalline honey crusher for cold processing of honey.
Results
The main results included:
- Increased revenue and savings through the new, more efficient production process and the building modifications that helped reduce operational costs, including energy/heating costs.
- Productivity was enhanced by streamlining the internal production processes.
- Reduced environmental impact through energy savings was achieved.
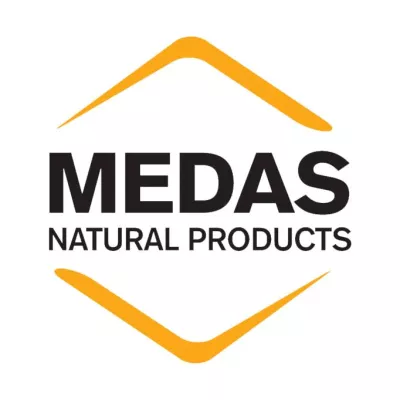
Promoter
MEDAS, s.r.o.
Funding
Total budget: 1 350 100 (EUR)
EAFRD: 506 288 (EUR)
National/Regional: 168 762 (EUR)
Private/own: 675 050 (EUR)
Ressources
Documents
Context
The story began in 2003 when the company Medas was founded to continue a longstanding family tradition of beekeeping. Today, the company is one of the largest beekeepers in Slovakia. Medas owns its own beehives and produces its own honey. However, their main activity is to purchase honey from other beekeepers and export natural bee honey products. The company buys honey directly from beekeepers across all of Slovakia and is able to trade a wide variety of honey, such as rape, flower, agave, forest and honeydew, by promoting the produce's ecologically pure origin. Some of the honey is also imported from foreign partners.
Medas places a strong emphasis on the quality of its products and applies regular controls to fully comply with strict veterinarian and hygienic standards and regulations across all areas of its business, including purchase, processing and storage facilities.
The company is currently among the leading Slovak producers and exporters of natural bee products. Its manufacturing and processing activities include a wide range of honey products, gastro packaging, consumer packaging, and wholesale and industrial packaging.
The company’s goal is to offer consumers a high quality, natural and nutritious product. To consistently achieve this, Medas is committed to investing time and resources to improve its products and modernise its processing machines and equipment. For example, a sales analysis indicated that a particular product was in high demand, but the company’s facilities needed improvement to respond more adequately to this increased interest.
Objectives
The main objective of the project was to support the company in procuring technology for the modernisation of its honey processing equipment, which aimed to increase the quality, quantity, safety and marketability of its products along with the competitiveness of the company overall. In addition, construction work was required to address a number of insufficient construction and technical conditions of the factory building, particularly its outer shell and roof to achieve energy savings.
Activities
The project involved the following activities:
- Implementing construction modifications on the perimeter of the production plant to improve the technical characteristics of the building. This involved insulating the factory to reduce the energy demand and heating costs of the building. The relevant work involved the insulation of the facade and roof structure and the replacement of external windows and doors.
- Procuring relevant technology and equipment to modernise and expand the company’s technology process. This included the purchase of several distinct items:
- A crystalline honey crusher with a tipper – a device that uses rotating knives to crush large lumps of cold honey. The advantage is that honey is not heated and processed cold, which preserves all of its natural properties.
- An automatic packing line consisting of filling, closing, labeling and reprinting information on the label and mass packaging.
- A thermal chamber - a room for heating honey in barrels or other packaging. It is built from self-supporting insulating PUR panels with a thickness of around 100 mm, a pallet racking system with a grid, a control unit and hot water air ventilation.
- A washing box for washing 12 barrels with hot water.
- Training and familiarisation of employees with the operations of the new production technology completed the funded project activities.
Main results
The main results included:
- Increased revenue.
- Savings were made through the new, more efficient production process, and the building modifications helped reduce operational costs, including energy/heating costs.
- Productivity was enhanced by streamlining the internal production processes.
- Reduced environmental impact through energy savings was achieved.
- Increased customer satisfaction by providing consistently high-quality honey products (cold processed honey).
- Improved technology and general improvements in and around the production plant created a positive work environment.
Key lessons
- Beekeepers should not hesitate to get involved in modernisation and improvement projects to introduce new, innovative technologies and procedures in the production process. By sharing information and knowledge, the experience and lessons from such projects would contribute to the development of the whole sector.